Índice
Sé que es difícil de creer, pero hay situaciones en las obras de construcción que ponen nuestros dispositivos Esders al límite y más allá. Por ejemplo, ataques de excavadoras, enterramientos de arena, cursos de natación o incendios.
Con el fin de preparar nuestros aparatos de medición de la mejor manera posible para cualquier tipo de situación diaria, en Haselünne también realizamos pruebas e inspecciones de durabilidad con regularidad.
Advertencia: Si carece de sentido del humor, le rogamos que no siga leyendo este artículo.
Ejemplos de nuestros dispositivos Esders bajo condiciones extremas
A continuación, presentamos algunos ejemplos de la vida cotidiana en la obra y le damos una idea de los procedimientos internos de Esders.
OLLI
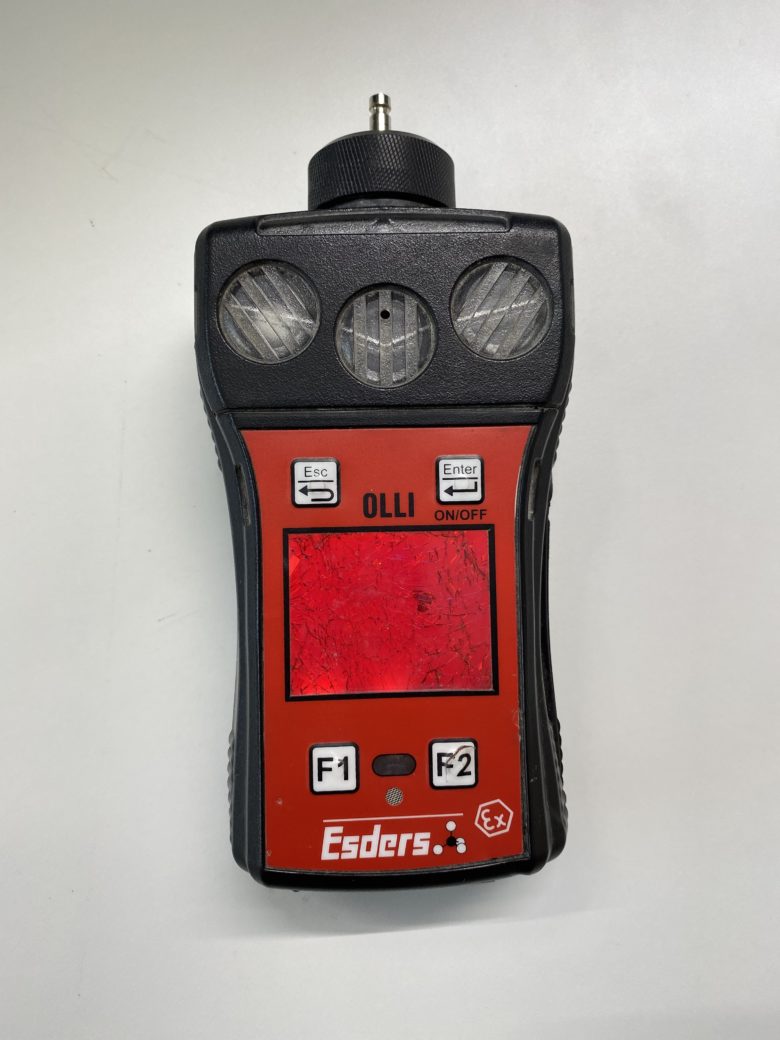
Nuestro precioso OLLI fue arrollado por una excavadora en un terreno relativamente blando. Todavía se puede encender y la alarma funciona, pero definitivamente ya no es posible trabajar con seguridad con este aparato, ya que la carcasa tiene grietas. La pantalla tampoco resulta ya convincente.
DruckTest GaWa
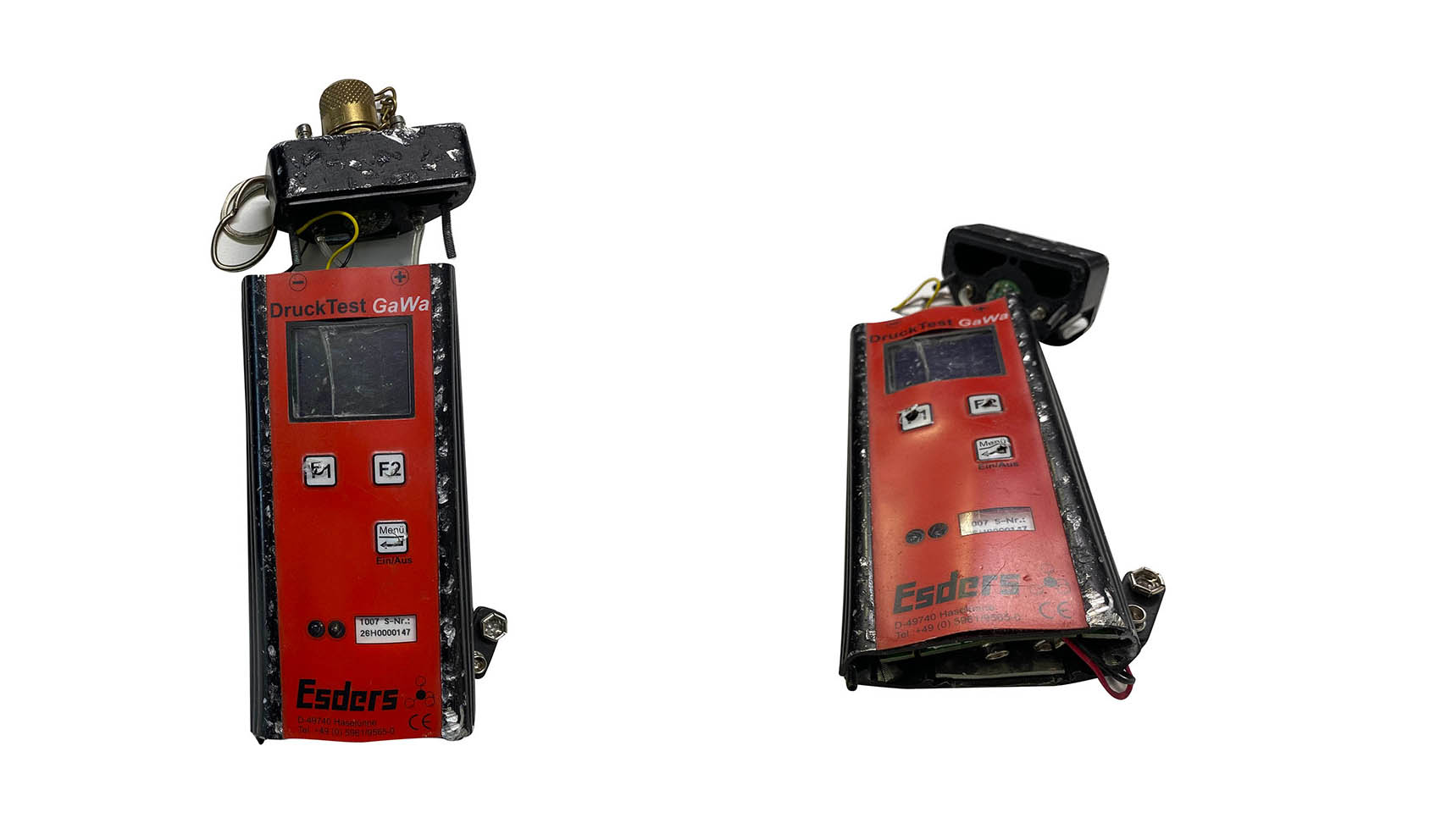
A continuación presentamos el DruckTest GaWa «Adelgazado», en el que también se utilizó una excavadora. La carcasa de aluminio ha cedido, pero el sensor incorporado sigue en buen estado, ya que el soporte del sensor está fresado a partir del sólido.
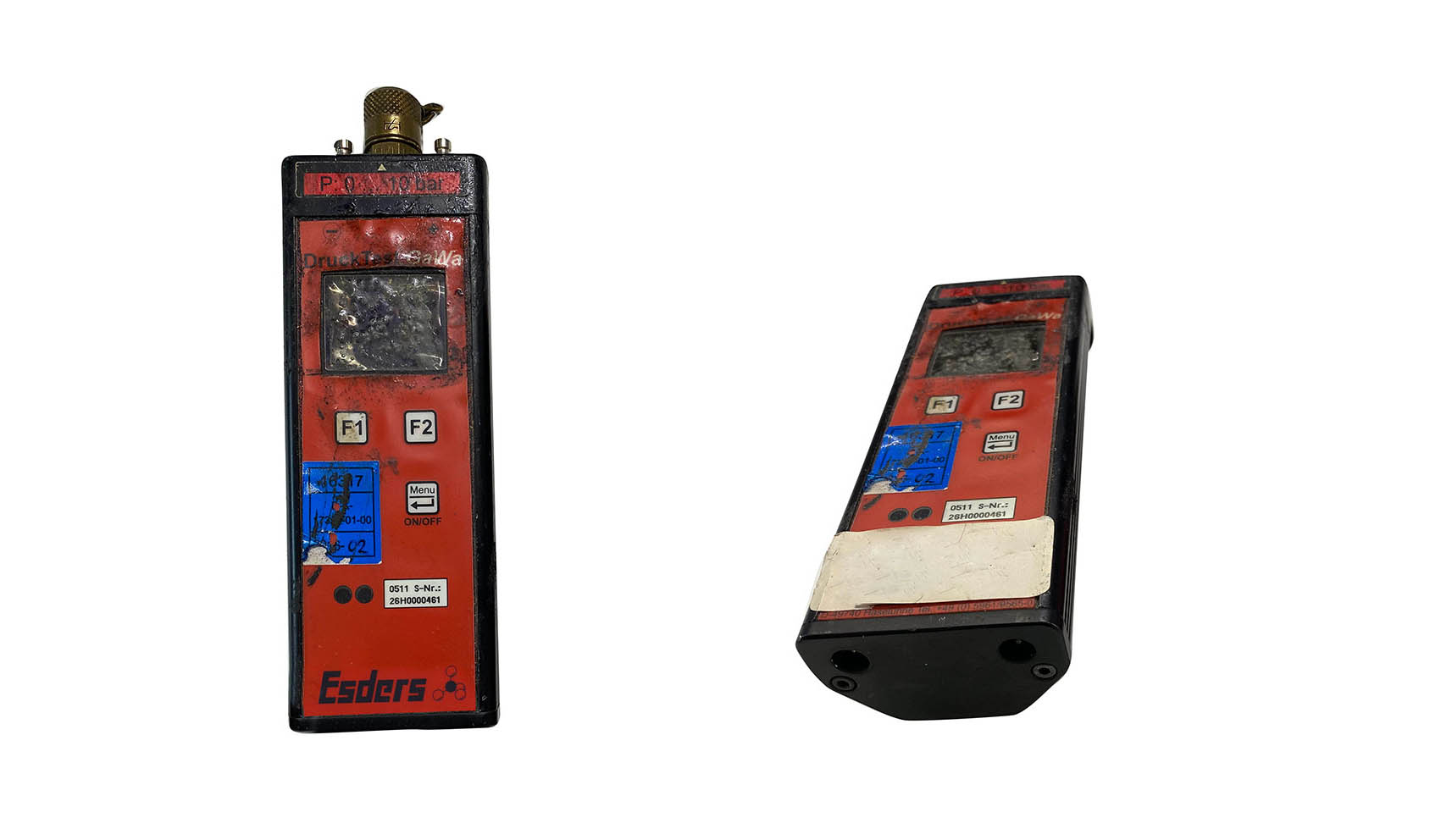
Además de la excavadora y los bulldozers, el fuego es un enemigo natural de nuestros equipos de medición. El DruckTest GaWa que se muestra aquí estaba en un coche que se incendió. Sorprendentemente, y qué casualidad, nadie recuerda cómo ocurrió exactamente. Le rogamos que se atenga estrictamente al rango de temperatura de los dispositivos Esders.
DruckTest memo
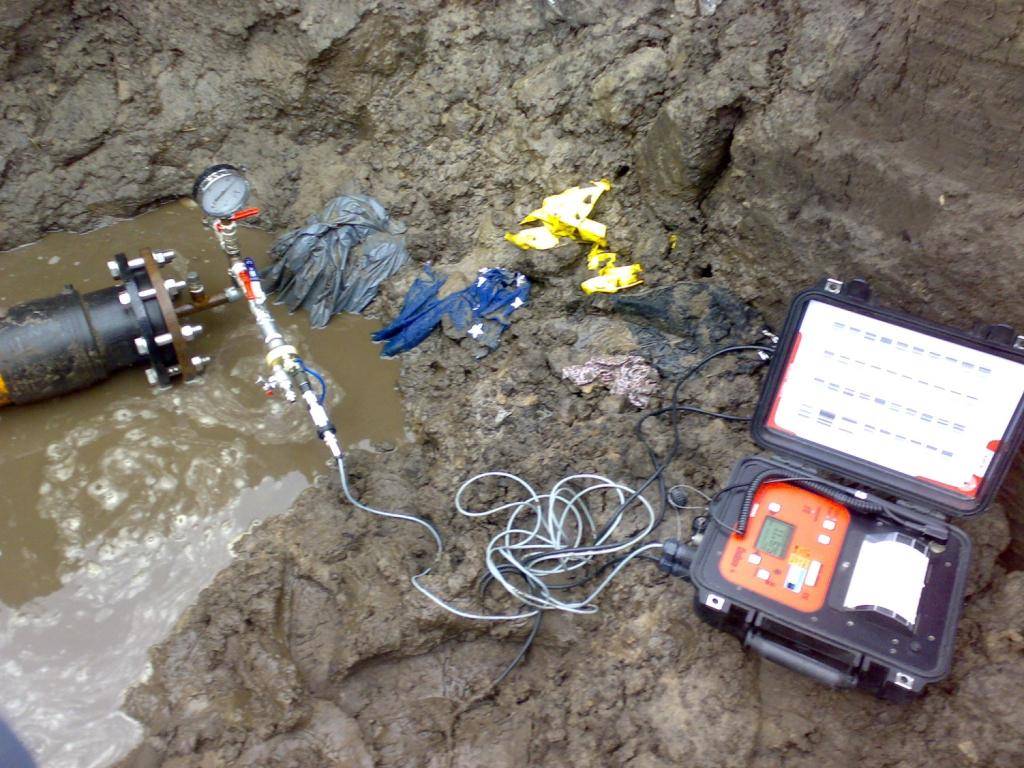
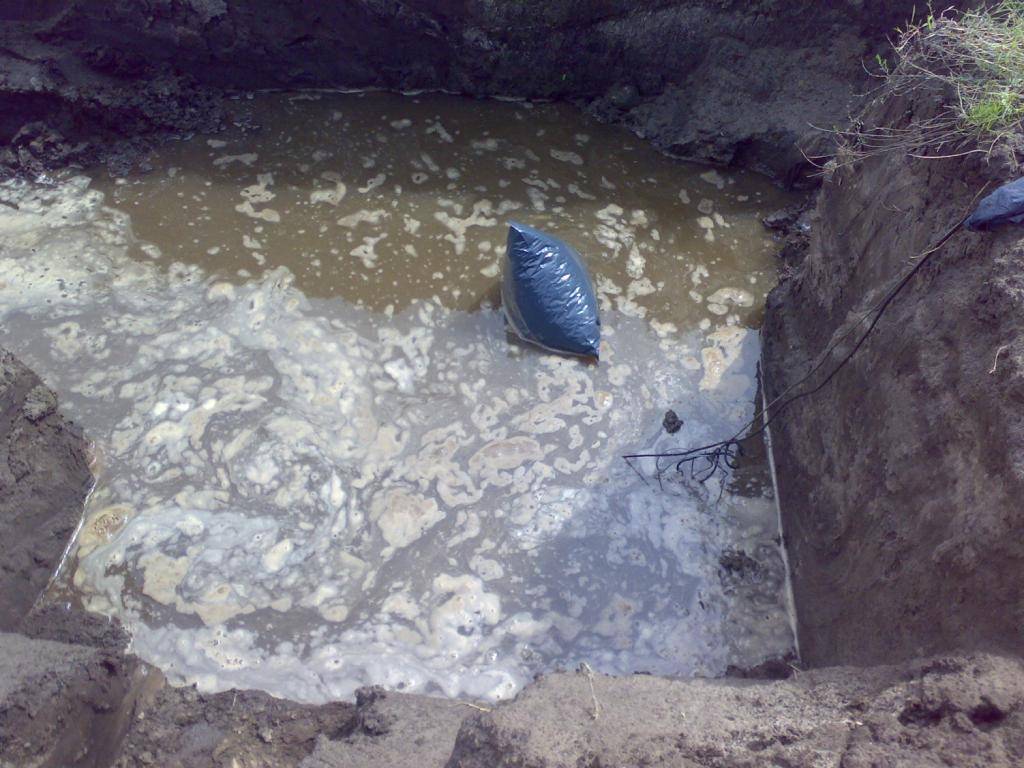
Los pozos de excavación no bien asegurados a veces plantean las mayores exigencias a nuestro equipo. Tras superar con éxito la prueba del caballito de mar* (con inmersión incluida), inscribimos el DruckTest memo en la insignia de bronce.
*Todos los niños de Alemania deberían aprender a nadar a los cuatro años. Al superar la prueba de natación recibimos la insignia del caballito de mar. El siguiente nivel en la clase de natación es la insignia de bronce, luego la de plata y así sucesivamente.
Pruebas para la dura realidad laboral - ¡Por favor, no intente esto en casa!
Algunas pruebas de nuestros dispositivos Esders las realizamos nosotros mismos en Haselünne con mucho gusto, como la caída libre desde la ventana de nuestro OLLI en fase de desarrollo. Al hacerlo, descubrimos que el montaje de la placa de circuitos en una posición todavía no es el óptimo.
Muy elegante en la fase de vuelo, pero la carcasa y los sensores sufrieron bastante con el impacto.
Sin embargo, estas auditorías internas ya no eran suficientes para nosotros en 2019, por lo que reunimos a un equipo de expertos altamente cualificados. Nuestros expertos realizaron diversos experimentos en el laboratorio en condiciones extremas.
Y por si aún no lo ha visto, aquí tiene las imágenes de nuestro laboratorio de pruebas.
Dejando las bromas a un lado, así es como se desarrollan y producen los dispositivos Esders al detalle
Cada vez que lanzamos al mercado un nuevo dispositivo Esders, llevamos a cabo un minucioso proceso de comprobación del producto desde el desarrollo hasta la entrega y mucho más. Los requisitos de los nuevos productos suelen venir del departamento de marketing, ventas o dirección, y son recogidos por la gestión de productos y discutidos en detalle con el departamento de desarrollo.
El siguiente paso es crear los documentos técnicos iniciales y desarrollar prototipos. En esta parte, interviene un experto en ATEX como desarrollador de hardware. Cabe recalcar que, no todos los dispositivos Esders requieren certificación ATEX en el campo de la protección contra explosiones.
El desarrollo de la carcasa de los dispositivos Esders
Cuando se desarrolla una carcasa nueva, la hermeticidad y manejo de la misma es muy importante. Mientras que antes intentábamos construir nuevas carcasas con modelos de madera o incluso de Lego, ahora lo llevamos a cabo mediante una impresora 3D, que nos ayuda en la comprobación de su manejo y hermeticidad y, si es necesario, nos permite hacer las optimizaciones oportunas.
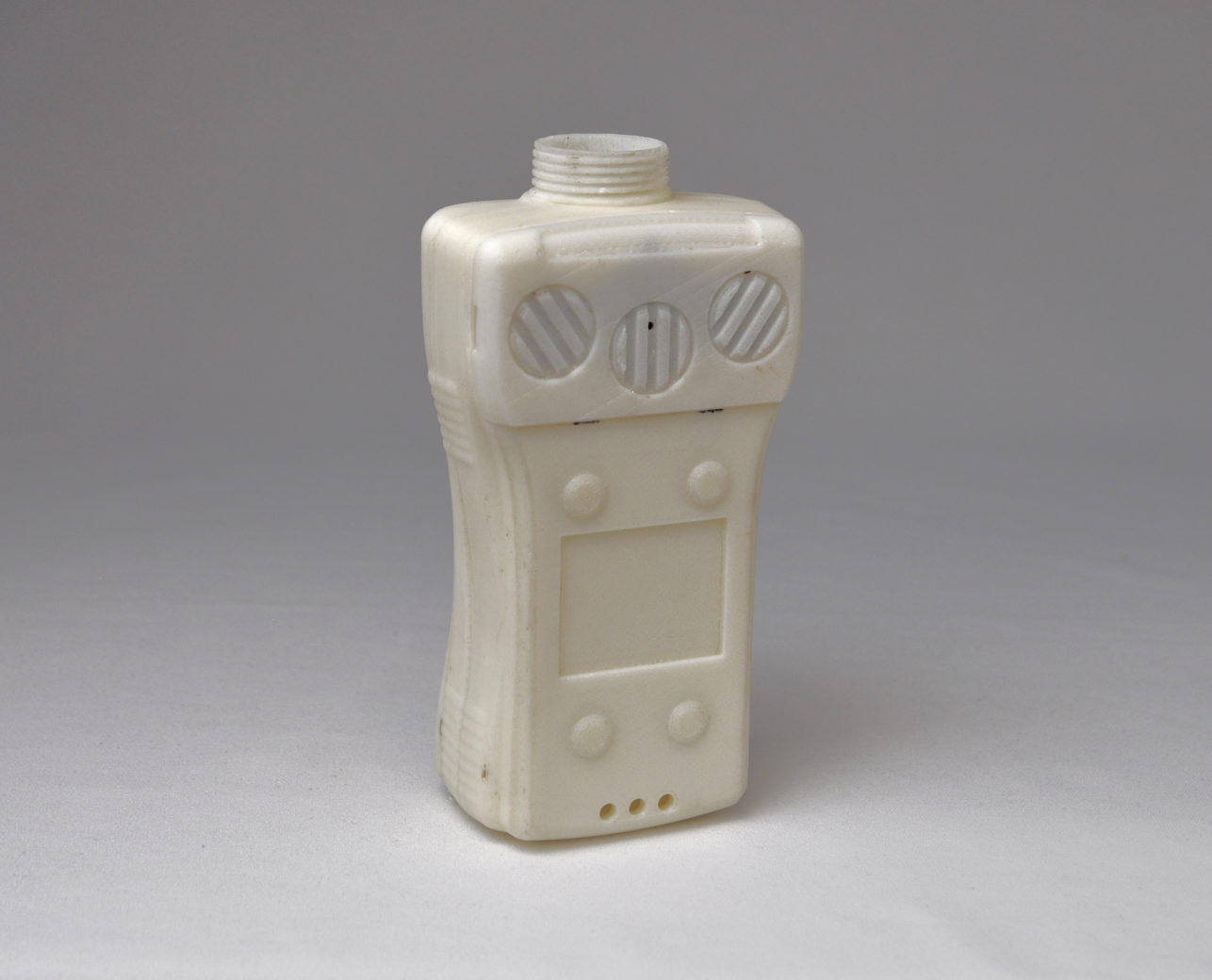
Una vez se ha desarrollado el diseño de un nuevo dispositivo, se construyen y prueban los primeros prototipos. En este proceso intervienen el departamento de control de calidad (QA) y el de desarrollo. Si se van a instalar nuevos sensores en un producto, que no se han utilizado en otros dispositivos de la empresa, se prueban en distintas condiciones ambientales (temperatura, humedad, presión atmosférica, concentraciones de gas) antes de utilizarlos.
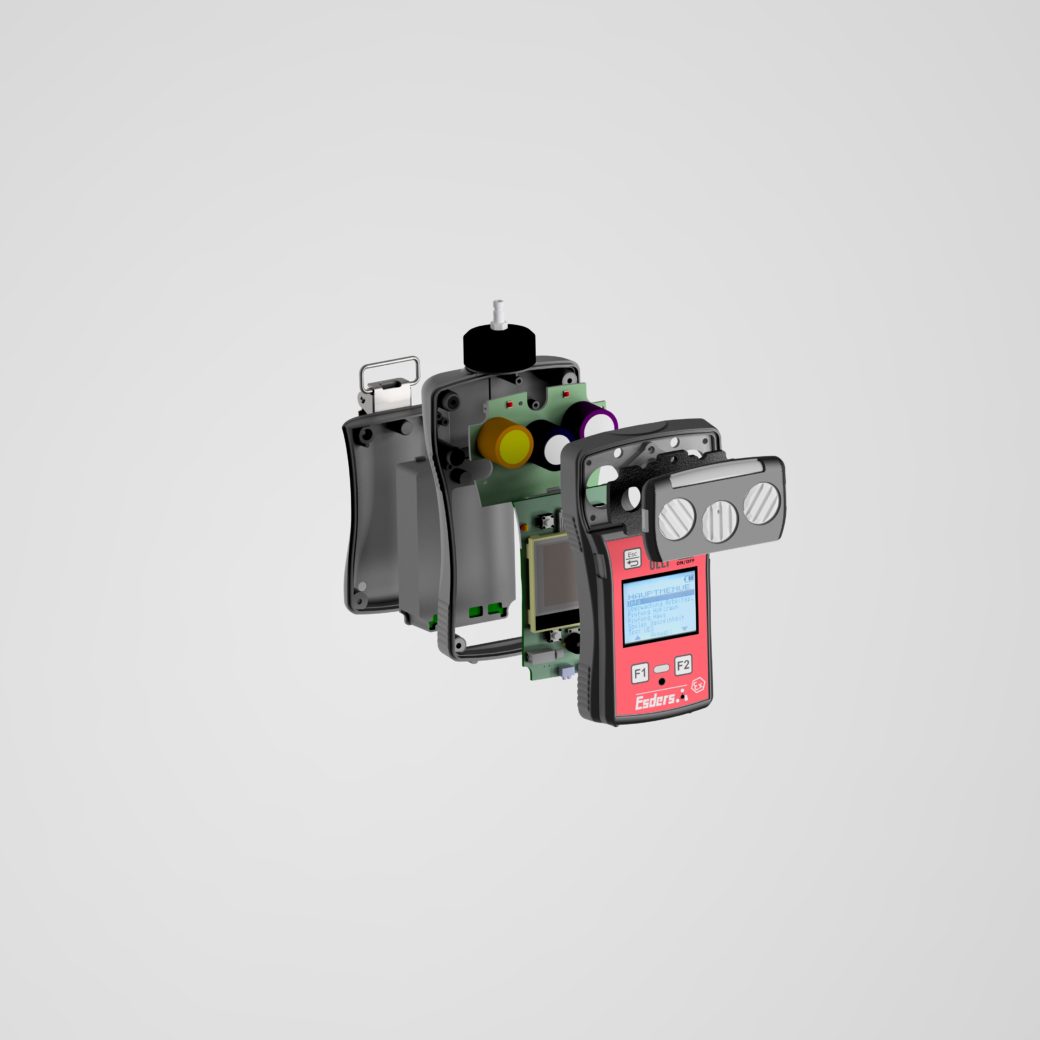
Pruebas de funcionamiento y usabilidad en la obra de los dispositivos Esders
A continuación, comprobamos la precisión de la medición en diferentes condiciones ambientales (temperaturas altas y bajas, diferentes humedades y diferentes presiones ambientales en el armario climático u otros equipos). Comprobamos el consumo de corriente en las distintas opciones del menú y probamos las baterías y la tecnología de carga.
A continuación, la producción y nuestro departamento de servicio llevan a cabo una prueba del ajuste y la calibración automáticos y una prueba del ajuste del cliente.
En un siguiente paso comprobamos la transferencia de datos a un software de PC o a la nube (si está disponible).
También comprobamos si los dispositivos son resistentes al agua y se realiza una prueba de caída para comprobar si la carcasa es «apta para obras».
Documentación, dibujos técnicos y diagramas de los circuitos
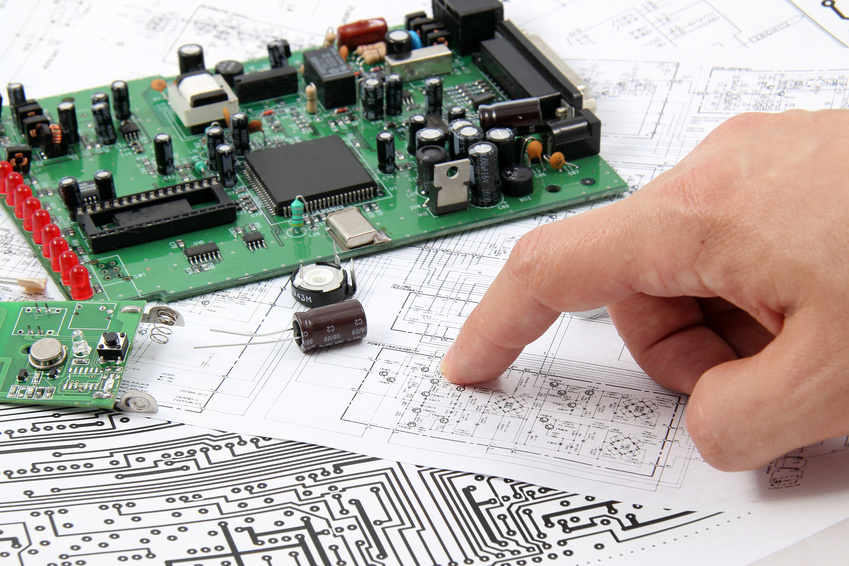
Para el centro de pruebas externo se prepara una amplia documentación, dibujos técnicos, esquemas de circuitos eléctricos y otros documentos del dispositivo de medición.
El departamento de producción elabora la denominada «serie cero» siguiendo las instrucciones de los desarrolladores implicados y poniendo a su disposición los documentos técnicos necesarios.
Basándose en la experiencia adquirida durante la construcción de la primera serie piloto, se crean las «instrucciones de montaje». En ellas se especifica detalladamente cómo debe construirse un producto. A continuación, el representante de ATEX lo comprueba y aprueba y, paralelamente, se instalan pruebas de control de calidad en la producción.
La serie cero se somete de nuevo a pruebas exhaustivas por parte del departamento de desarrollo de control de calidad (aspectos funcionales y de seguridad), así como de gestión de productos y ventas (requisitos del cliente).
Al mismo tiempo, ya se están creando los llamados «prototipos», que se envían a un laboratorio de pruebas externo para su comprobación.
Una vez superadas con éxito las pruebas externas, el laboratorio de pruebas externo expide el certificado de pruebas de tipo UE.
A partir de ese momento, todas las demás modificaciones del producto relacionadas con la seguridad deben ser aprobadas por el laboratorio de comprobaciones externo, en cada caso mediante modificaciones del certificado de prueba de tipo UE expedido.
Si todo está correcto, se inicia la producción en serie
En la producción en serie en curso, la secuencia de producción sigue siendo la misma y la calidad es supervisada por el departamento de producción de control de calidad. Si es necesario realizar cambios, éstos sólo pueden llevarse a cabo tras la inspección del representante de ATEX. También comprueba si es necesario modificar el certificado de examen UE de tipo.
La garantía de calidad de los dispositivos Esders no termina con la entrega del producto
Muchos dispositivos vuelven a nuestra fábrica para un servicio anual o son revisados regularmente por nosotros durante nuestro servicio móvil. Además, registramos como quejas en nuestro sistema ERP cualquier comentario negativo del cliente procedente del servicio técnico. Esto nos proporciona una base de datos muy buena para evaluar la calidad de nuestros dispositivos a lo largo de todo el ciclo de vida del producto.
De esta forma, sabemos bastante bien qué componentes, funciones, etc. siguen funcionando bien después de muchos años de funcionamiento y cuáles ya no tan bien, y actuamos en consecuencia.
Desde la primera idea hasta el producto hay un largo trecho. Pero sólo así podemos asumir los requisitos de nuestros clientes y aplicarlos con alta calidad. Nuestro objetivo es seguir analizando y mejorando los procesos.